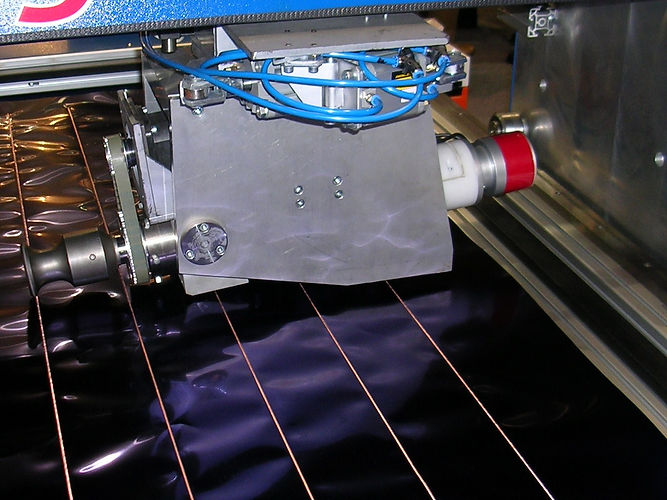
What is Ultrasonic Welding?
Ultrasonic welding is a sophisticated technique used to join materials, typically thermoplastics, through high-frequency ultrasonic vibrations. This method allows for precise, fast, and efficient bonding, making it a preferred choice in various industries. The process involves the conversion of electrical energy into mechanical energy, generating ultrasonic waves that produce localized heat through friction at the joint interface.
The History of Ultrasonic Welding
The concept of ultrasonic welding dates back to the 1940s, but it wasn’t until the 1960s that it gained widespread industrial application. Initially used in the automotive and electronics sectors, the technology has since expanded to areas like medical devices, packaging, and consumer goods. Over the decades, advancements in ultrasonic technology have enhanced the capabilities and applications of this joining process.
How Ultrasonic Welding Works
The ultrasonic welding process begins with the placement of two plastic parts in a fixture. An ultrasonic transducer converts electrical energy into mechanical vibrations. These vibrations are transmitted through a sonotrode (a tool that focuses the ultrasonic energy) to the joint interface of the materials. The high-frequency oscillations generate heat due to friction, softening the materials and allowing them to fuse upon applying pressure.
Key Components of Ultrasonic Welding Equipment
To fully understand ultrasonic welding, it's important to recognize the equipment involved:
-
Ultrasonic Generator: Converts electrical energy into ultrasonic energy.
-
Transducer: Converts the electrical energy from the generator into mechanical vibrations.
-
Sonotrode: Focuses the ultrasonic energy onto the workpieces.
-
Fixture: Holds the parts in place during the welding process.
Advantages of Ultrasonic Welding
Ultrasonic welding offers several advantages that make it a preferred joining method in many applications:
-
Speed: The process is extremely quick, often taking just milliseconds to complete.
-
Energy Efficiency: Ultrasonic welding consumes less energy compared to traditional welding methods.
-
Minimal Heat Affected Zone: The localized heating results in less thermal distortion of the materials being welded.
-
Environmentally Friendly: The process typically does not require adhesives or solvents, making it a cleaner option.
Applications of Ultrasonic Welding
Ultrasonic welding is utilized across a variety of industries. Some of the most common applications include:
-
Automotive: Used for assembling components like dashboards, fuel tanks, and wiring harnesses.
-
Electronics: Essential for connecting wires, battery packs, and circuit boards.
-
Medical Devices: Critical for assembling components in devices like syringes, IV bags, and surgical instruments.
-
Packaging: Employed in the creation of blister packs and sealable pouches.
Challenges in Ultrasonic Welding
While ultrasonic welding has numerous benefits, there are also challenges that engineers must address:
-
Material Compatibility: Not all materials can be ultrasonically welded together. Engineers must ensure compatibility for effective bonding.
-
Joint Design: The design of the joint significantly impacts the quality of the weld. Poor design can lead to weak bonds.
-
Equipment Costs: The initial investment in ultrasonic welding equipment can be high, which may deter some businesses.
Ultrasonic Welding vs. Other Welding Techniques
When comparing ultrasonic welding to other joining methods like laser welding, resistance welding, or traditional adhesive bonding, several factors come into play:
-
Speed: Ultrasonic welding is faster than most other methods.
-
Heat Control: It generates less heat, reducing the risk of thermal damage.
-
Material Versatility: While some methods are limited to certain materials, ultrasonic welding is effective with a variety of thermoplastics.
Future Trends in Ultrasonic Welding
The future of ultrasonic welding looks promising, with several trends emerging:
-
Increased Automation: As industries move toward automation, ultrasonic welding systems are becoming more integrated with robotics for enhanced efficiency.
-
Advanced Materials: Research into new materials that can be welded ultrasonically is ongoing, potentially expanding its applications.
-
Smart Technology: The incorporation of IoT and machine learning in ultrasonic welding systems is anticipated to improve process control and quality assurance.
Conclusion
Ultrasonic welding stands out as a vital technology in modern manufacturing. Its unique ability to provide fast, efficient, and clean joining of materials makes it an indispensable tool across multiple industries. As technology continues to advance, the applications and capabilities of ultrasonic welding will likely expand, paving the way for innovations in production processes. Whether in automotive, electronics, or medical fields, ultrasonic welding is poised to play a significant role in shaping the future of manufacturing.